1. Overview
Microsoft Dynamics 365 Business Central / NAV offers a wide range of useful production support. It includes the ability to plan manufacturing capacity.
A product being manufactured is linked to two critical pieces of information:
- Bill of materials (BOM) that describes the components, which comprise the item under production and
- Routing that characterizes the process requirements
It is the routing that facilitates planning capacity and also forms the basis of this write-up.
Benefits of production routing:
Production routing enables an enterprise to evaluate the efficiency of their manufacturing process. It aids detecting those steps in the production process that represent a constraint because of demand exceeding the capacity or when it is underutilized.
- In Business central there is a provision to define the production operations in routing setup.
- The routing is the basis of process scheduling, capacity scheduling, scheduled assignment of component items needs, and manufacturing documents.
- A routing holds master data that defines the operations/process requirements in terms of Machine Centre and Work Centre for a given produced item.
- The equipment usage sequence will be defined as operation number and every operation previous and next operation number will be defined in routing lines.
- The standard operation/process duration for each operations using a machine or work Centre can be defined as setup time, run time, wait time, move time, queue time etc.
- After creating a routing, same can be defined in item master or stock keeping unit master.
2. Routing
2.1 Routing Card
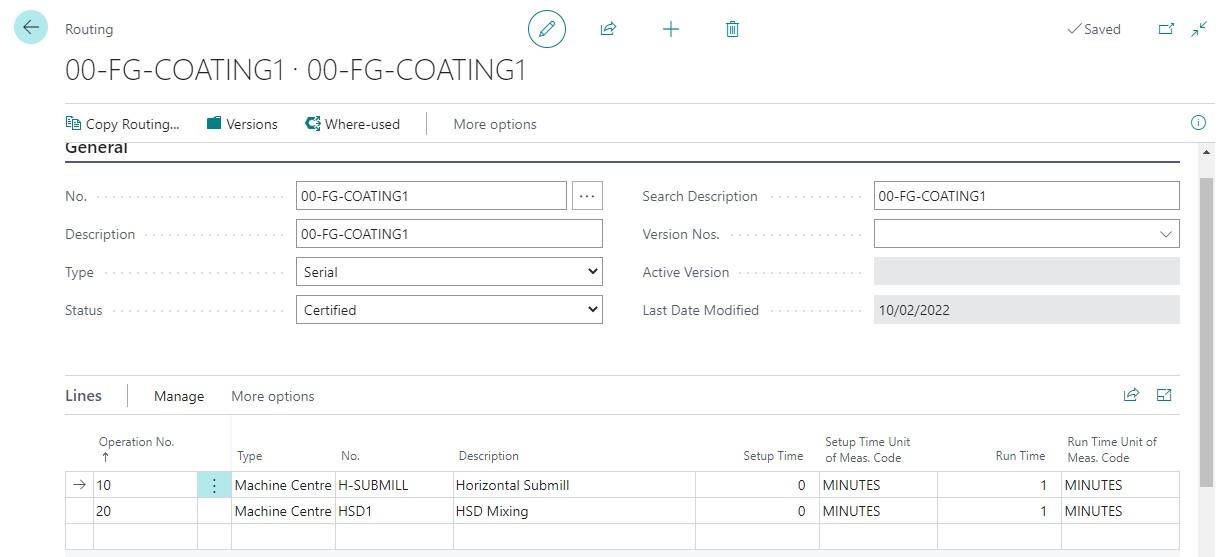
2.1.1 Routing Header
Fields on Routing Header:
Fields |
Description |
No. |
This is a unique identifier code for the routing. You can enter a maximum of 20 characters. This includes both numbers and letters. |
Description: |
Description for the routing header that makes it easier to recognize its purpose. You can enter 30 characters. This includes both numbers and letters. |
Type |
Specification that defines the routing as serial or parallel.
- Serial – Indicates that the routing operations are performed sequentially as defined in routing lines.
- Parallel – Indicates that two separate, unrelated operations can be performed at the same time. The operation sequence is followed as per the value in “Next Operation” field. For more information, refer to the “Parallel Scheduling” topic in the “Routings Advanced Features” lesson in this training material.
|
Status
|
Status of a routing. The following are valid statuses:
- New –The status is set automatically to New when you create a new routing. With new routings, you can edit the contents of the routing fields.
- Certified – You manually set the status of a routing to Certified when it is ready for production. Only certified routings are used for production orders and production planning. You cannot edit the fields of a routing if it is certified.
- Under Development – You manually set the status of a routing to Under Development when you want to edit it. Changing a routing to this status makes it possible to edit the routing fields. After you finish your edits, you must change its status back to Certified if you want to use the routing for production and planning again.
- Closed – You manually set the status of a routing to Closed when it is no longer used.
|
Search Description
|
Search criteria for a routing when you do not remember its number. The field derives from the description, but you can edit it to create a name that is easier to remember.
This field can have a maximum of 30 characters.
|
Version Nos
|
Specifies the number series to use to create a new version of this routing. The program automatically takes the next number from this number series to create a new version. If you leave this field blank, you must manually assign the version code. |
Active Version
|
The current version that is used. The starting date determines the active version. Also, the status of the active version must be Certified. |
Last Date Modified
|
This field updates to the current system date (not the work date) when a routing is initiated or changed. |
2.1.2 Routing Lines:
Field Details in Routing Line:
Fields |
Description |
Operation No. |
Operation number for the routing line. Every line of the routing has an operation number, which the program uses for various references. You can enter no more than 10 characters. This includes both numbers and letters. The program sorts operations in the order of the operation number. We recommend that you leave a gap between operation numbers, such as 10, 20, 30, and so on. This makes it easier to insert new operations between existing ones. |
Next Operation No. |
Specifies the next operation number. You use this field if you use parallel routings. |
Previous Operation No. |
Specifies the previous operation number, which is automatically assigned. |
Type |
The capacity type that is used for the operation. You can specify one of two types:
- Work Centre
- Machine Centre.
Certain information copies to the routing line that is based on the type that you select.
If you select Work Centre, the following field information copies to the routing line:
- Setup Time Unit of Meas. Code
- Run Time Unit of Meas. Code
- Wait Time Unit of Meas. Code
- Move Time Unit of Meas. Code
Machine Centres link to a Work Centre. If you select Machine Centre, the following field information copies to the routing line (if defined):
- Setup Time and Setup Time Unit of Meas. Code
- Wait Time and Wait Time Unit of Meas. Code
- Move Time and Move Time Unit of Meas. Code
- Fixed Scrap
- Scrap %
- Send-Ahead Quantity
- Minimum Process Time
|
No. |
Select the Machine Centre or Work Centre from the master list based on the value in field Type. |
Work Centre No. |
Specifies the Work Centre No. linked to the Machine Centre when “Machine Centre” is defined in “Type” field and “No.” field.
|
Description |
Name of the machine centre or work centre. |
Routing Link Code
|
This species a linking code between a routing operation and a component in production BOM. This indicates that the component item is consumed in a particular operation where the same routing link code is defined in a routing operation and a production BOM component. |
Scrap Factor % |
You can define the Scrap% on operations if the operations generate scrap. This will increase the components required quantity for the current operation and the previous operations as well. This will also increase the calculated production output quantity in production journal for compensating the scrap. If you are using scrap % then its important to link the operations with BOM components using Routing link Code. Not doing so may result in component quantity requirement may show excess quantity. |
Fixed Scrap Quantity
|
Scrap related to an operation can also be defined as a fixed quantity. It has the same effect as the scrap factor % but with the difference that it is specified in an absolute quantity instead of a percentage. |
Lot Size |
Specifies the number of items that are included in the same operation at the same time. The run time on routing lines is reduced proportionally to the lot size. For example, if an operation is set to 8 minutes and the lot size is 4 then it takes 2 minutes per unit. If this field is left as 0 then Dynamics NAV assume that it should be 1. |
Run Time |
This is the operation run time required for the selected resource, for producing one unit of the item in production order. |
Setup Time |
This is the setup time to be defined for a production order. The setup time is to be defined for the entire production order but not per unit production. |
Wait Time |
The time that is required between the processing steps, such as drying processes. APICS defines wait time as "the time a job remains at a work Centre after an operation is finished until it is moved to the next operation. It is often expressed as part of move time." |
Move Time |
The time a production lot or batch spends in transit from one operation to the next. |
Setup Time Unit of Meas. Code
|
Specifies the unit of measure code that applies to the Setup time of the operation. |
Run Time Unit of Meas. Code |
Specifies the unit of measure code that applies to the run time of the operation. |
Wait Time Unit of Meas.
|
Specifies the unit of measure code that applies to the Wait time of the operation. |
Move Time Unit of Meas.
|
Specifies the unit of measure code that applies to the Move time of the operation.
|
Concurrent Capacities
|
This field specifies how many units of the selected resource are used to perform the operation. For example, two people allocated to one packing operation will halve the run time. |
Unit Cost Per |
The task-related production cost to use if the unit cost of the operation is different from the unit cost on the work Centre card. If you decide to enter the cost on each routing operation line, you must select the Specific Unit Cost field on the work Centre card. This is available for work Centres only. For machine Centre operation lines, you can specify the unit cost only on the machine Centre card.
|
Standard Task Code
|
Standard task for the operation. When you select a standard task code, the description of the standard task is copied to the Description field. If you save tools, personnel, descriptions, and quality measures under the standard task, this information is copied to the routing line.
For more information on standard tasks, refer to “Additional Manufacturing Topics” in this training material.
|
Minimum Process Time
|
Minimum time that is required by the machine for processing. This is for information purposes only and does affect any processes. |
Maximum Process Time
|
Maximum time that is required by the machine for processing. This is for information purposes only and does affect any processes.
|
Send-Ahead Quantity
|
Minimum Quantity of the current operation that must be finished before the next operation can start before completion of all quantity in current operation. This
|
Throughput Time
There are two types of throughput time: productive and non-productive. Each type consists of other time components.
Productive Time
Productive time consists of the setup time and run time:
- Setup Time – The time that is required to set up the machine or work Centre to convert from production of the last good item in a lot to the first good item of the next lot.
- Run Time – The time that is required to process or manufacture an item for a specific operation. Run time does not include setup time.
Non-Productive Time
Non-productive time consists of wait time, move time, and queue time as follows:
- Wait Time – The time that is required between the processing steps, such as drying processes. The wait time is the time a job remains at a work Centre after an operation is finished until it is moved to the next operation. It is often expressed as part of move time.
- Move Time – The time a production lot or batch spends in transit from one operation to the next.
- Queue Time – The time that production lots or batches wait at a work Centre or machine Centre before setup and processing. This occurs when a released production order arrives at a facility, but the facility is already busy processing another operation. In other words, queue time is used to represent work in front of a facility rather than behind it. This can indicate a production line that is not in balance or that has bottlenecks. If queue time is not used, the scheduled generated for a production order might be too optimistic. This is because the system schedules each order as if it is the only order in the factory. Therefore, you can use queue time to improve the accuracy of order scheduling based on real production times.
Routing Versions
You can have several versions of the same routing. The structure of a routing version corresponds to the structure of a routing. The routing version consists of a routing version header and routing lines. A version code identifies each routing version. You can define versions by their starting date. A routing version automatically becomes active on its starting date. All versions with a starting date older than this date become invalid. To become active means that the program uses the version automatically in place of the routing as of that date.
The advantages of using routing versions include the following:
- The ability to schedule the implementation of a new version by setting its starting date. Because the program automatically uses the new version when the starting date is reached, the process engineer does not have to remember when to switch from one version to the next.
- Because the program automatically uses the correct version of a routing for any given date, there is no need to change the product structure by changing the routing that is associated with items.
- The old version of the routing is retained in the database. The engineer can use this historical information, such as the date when a routing was changed, to determine if routing changes achieve their desired effect.
Copy Routing Version
To make the creation of routing versions more efficient, you can use the following functions on the Actions tab of the routing version card:
- Copy Routing Header – Copies the base routing lines to the current routing version.
- Copy Routing Version – Copies the routing lines from another routing version that you select to the current routing version.
After the operations are copied to the new routing version, you can make any necessary changes.
2.1.3 Routings Advanced Features:
Microsoft Business Central provides a number of advanced routing features. These include the following:
- Routing link codes
- Parallel Scheduling
- Send-ahead quantity
Routing Link Codes:
Use routing link codes to link a component that is defined on an item's bill of material (BOM) to an operation on the item's routing. This lets you specify at which step (operation) in the manufacturing process the components are flushed or removed from inventory. If you do not specify this, all components are removed at the start or the end of the production order. Routing link codes support greater just-in-time (JIT) functionality and frequently are used in long processes.
You must establish routing link codes on the routing lines prior to their entry on production BOM lines. MRP uses the routing link codes to schedule components that are based on the start date of the operation that requires them. The flushing method that you select on the component item cards affects when the components are removed from inventory.
Component Flushing Method |
Removal from Inventory |
Manual |
Only when the user posts through the consumption or production journals. |
Forward |
Forward When the routing step is started. |
Backward |
When the routing step is finished. |
Parallel Scheduling:
Parallel scheduling means that two separate, unrelated operations are performed at the same time. Parallel operations reduce throughput time, increase efficiency, and help reduce the complexity in the BOM structure.
Send-Ahead Quantity:
The send-ahead quantity feature lets users specify for each routing operation, a portion of the lot or batch that is sent to the next operation. The next operation starts when the send-ahead quantity is produced.